Click HERE here
to join the Metfab e-mail list to receive the latest news
Click HERE here
to view pictures of some of our specialty work
December, 2016 Newsletter
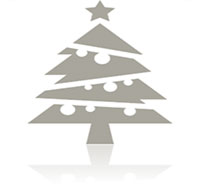
Metfab Metals----2016: Even More Progress
MERRY CHRISTMAS & A VERY HAPPY
HOLIDAY SEASON
Month: |
Our 2016 Newsletters/Subject |
(All Archived on our website) |
January |
Super Success |
Speaks for itself. |
February |
Efficiency; Capacity |
We got better. |
March |
AESS Update |
We’re the experts! |
April |
Accuracy |
We got better. |
May |
Cooperation |
We got better. |
June |
Podium Steel; Major Mullions |
Real pretty! |
July |
Samples |
Anytime you want! |
August |
VMUs; Visual Mock-Ups |
A regular item here! |
September |
Retro-Fit; Retro-Clad |
Another bit of our expertise! |
October |
Diversity |
A unique look! |
November |
3-D Printers/Metals |
Coming innovations! |
Looking back over the breadth of what we worked on this passing year, it has already been a “great” year for this American company. Just a brief review of the titles----and content----of these monthly reports to our customers (present & future) amply shows that what was already great here at Metfab Metals, LLC is now getting greater in meaningful increments, even before our new government assumes control with its quiver of future greatness concepts & ideas.
As we said last month about 3-D printing, we want to be “ahead of the wave” for you and so we are focused on all the trends in our industry. We will not be automated out of business----or fall behind in any other fashion. Other months, we stressed our nimble service to all our customers, back over the past 30+ years!
We thank all our IT guys for the insights and “heads-up” to all of us working each day with currently-available technology. And for what they are “playing with” (an IT term, not mine) each day to make us better. We presently have all the cutting-edge technology in our shops today and the young brains to use it best for you. [Watch for our new inter-active website to further speed up how we can work together seamlessly.]
Look over the litany of topics we sent out to all of you this past year, covering everything from Success to Accuracy to Cooperation to Samples to Diversity---and in which we tried to convey so much more. Follow us in 2017 and beyond, as we plan ahead to be ever “greater” and ever better meeting your needs.
All of us here at Metfab Metals know our industry (& yours) and always focus on the coming technologies so that we can better handle your job’s needs TODAY! And be even “greater” tomorrow, and next year, and each year after that! We are here to service your evolving needs for decades to come.
A final note at this year’s end---our established process requires planning with precise and workable specs BEFORE we generate an agreed-upon PO for the final fabricated metal needed at the modern jobsite (1). We ask our regular customers to involve us more in this planning stage. AGAIN please recognize--ours is a NO-cost offer in which we take a look at what metals are needed and give the Owner & Design Team a chance to take advantage of our hands-on, current experience as to what works best in our aspect of the plans (then yet to be finalized). So, when your busy schedule allows, look back over what we catalogued for you in our 2016 Newsletters. We are doing all of this for others now. We want to do even more for YOU in 2017.
Metfab Metals has decades of experience producing all the various metal parts/assemblies needed for YOUR retro jobs that can serve to make them go smoothly from its earliest stages------------and end successfully!
Call us; you’ll soon see we produce.
Call me for ALL your METALS questions. If I can't answer it, I have all the needed "sources" to do so!
Jim Murray, C.O.O. 973-675-7676
[email protected]
UPDATE:
Hudson Yards, NYC, NY ----- Last year in this space, we reported on this huge West Side development and our work there throughout 2015. Now we report as an update that we have supplied even more AESS mullions throughout 2016. We are continuing other needed fabrications for the various other buildings making up the myriad structures rising there---and have orders running through 2017 and into 2018.
1. Building Design & Construction (online magazine) at www.bcdnetwork.com (September 16, 2009) by Mark Baker, Pres., IBA Consultants:
NOW, Metfab Metals is your single best fabrication answer, not only for quality custom and production Heavy-Gauge AND Light-Gauge metal parts, but also when your job requires AESS in all its MANY forms, finishes and applications!
Happy Holidays!
All Good Things to YOU in 2017!!!

November, 2016 Newsletter
3-D Printers May Change How We All Make Metal
Parts for Your Jobs Too
(Maybe Sooner Than You Might Think)!
Few metal fabricators have more expertise than Metfab Metals, LLC but we also watch developments in such things as 3-D printing. We want to be “ahead of the wave” for you and need to be focused on all the trends in our industry. We do not want to be automated out of business. We also don’t want to be unable to nimbly service our customers as we have done for 30+ years! Here’s a good example of what we watch.
SLM Solutions NA, Inc. of Novi, Michigan (1) shows what a German company is already doing with computer-driven lasers to make replacement parts to order via “3-D printing”. The impact this may have on “after market” supplies and suppliers cannot yet be foretold by any but the best futurist thinkers! Take a look for yourself!
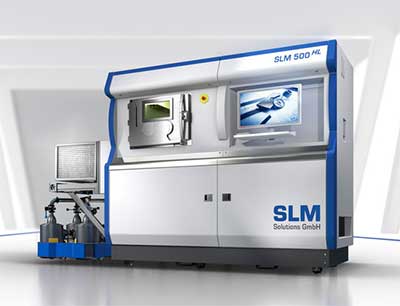
[SLM's newest quad laser 3-D printer]
SLM is to be thanked for this insight and “heads-up” to all of us working each day with currently-available technology. Ten years from now, we may all be wondering how we fulfilled our customers’ needs in 2016, as we were such seeming Luddites then!
We presently have all the cutting-edge technology in our shops today and the young brains to use it best for you. [Watch for our new inter-active website to further speed up how we can work together seamlessly.]
We can quote now several observations about this existing green “laser sintering”—and even more futuristic—technology! Such as,
Direct Metal Laser Sintering (DMLS) uses a precise, high-wattage laser to micro-weld powdered metals and alloys to form fully functional metal components from your CAD data. DMLS eliminates time-consuming tooling, and creates complex geometries not possible with other metal manufacturing processes. Made from materials like Inconel, Aluminum, Stainless Steel, and Titanium, DMLS parts are strong, durable, and heat-resistant. DMLS parts are also denser than investment casted metal parts. This accurate metal 3D printing process provides fine feature detail, making it ideal for complex oil and gas components, custom medical guides, consolidated aerospace parts, and tough functional prototypes.(2) ………….(partial text omitted).
Raw parts have a surface finish comparable to a fine investment cast part, but expert finishing services are crucial for a successful end-use component. This is partly why DMLS is not feasible for many companies and firms to take in-house with their own 3D printing operations, but [we have] the resources and experience you need. We offer a variety of professional finishing options, such as media blasting, electroplating, polishing, and CNC machining. Parts can also be heat treated in order to maximize mechanical properties. (3)
|
But what does this “3-D metal printing (sintering)” actually mean for you? Well, a part can take many forms, all defined by the specs issued for its fabrication. Most simply, it can just mean making of new parts in a better way not available at former times. It means fabrication by a new protocol---direct from your CAD drawing to the full one-step, melded fabrication of the “finished” product.
Regularly today, our entire building/fabricating process is guided by one word: GREEN, that is, the owners want to build the building in a far more energy efficient manner, entitling them to LEED recognitions, with projected power & maintenance savings offsetting higher fabrication costs. We hear these conversations more frequently now than ever with each new, groundbreaking job, such as the myriad ideas informing Hudson Yards in NYC. As we here at Metfab Metals know our industry (& yours) and always focus on the coming technologies, we can better handle your job’s needs TODAY! This can mean for you that we can---and do---supply ALL the metal products for your innovative project. Currently, we are supplying various aspects of such cutting edge fabricated metals for Hudson Yards and more.
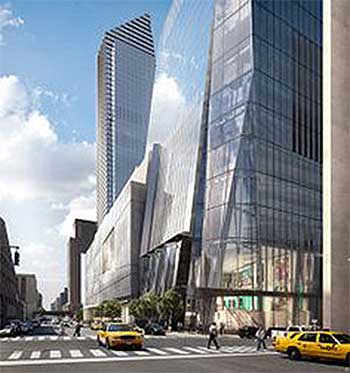
[Rendering of just part of Hudson Yards (NYC,NY), the largest private development in history. Picture is courtesy of the Related Companies.]
Also importantly, this process requires planning with precise and workable specs BEFORE we generate an agreed-upon PO for the final fabricated metal needed at the modern jobsite, we ask our regular customers to involve us more in this planning stage. Ours is a NO-cost offer in which we take a look at what metals are needed and give the Owner & Design Team a chance to take advantage of our hands-on, current experience as to what works best in our aspect of the plans (then yet to be finalized). Months ago, here in this space, we talked about the value of VMU’s and PMU’s and how we offer that service. This is an item that can be considered a wise investment on many upscale jobs. (5)
We often take an order for a VMU or PMU (6) at an early pre-construction stage so the design team can see exactly they want, perhaps see how it reacts to the elements and issue revised specs, drawings and PO’s along those adjusted lines. In our long experience, a VMU is an ultimately cost-effective way to qualitatively test whether your specs have a problem well-worth solving before committing to building out all the fabricated steel your design calls for, as well as ancillary parts such as glass, color, fillers, nuts & bolts and much more.
1. See this article and supplement online at www.globalspec.com/supplier/about/SLMSolutionsNA
2. Courtesy of Stratosys, www.stratasysdirect.com/solutions/direct-metal-laser-sintering (2016)
3. Ibid as #2 footnote. Courtesy of Stratosys, www.stratasysdirect.com/solutions/direct-metal-laser-sintering (2016)
4. Building Design & Construction (online magazine) at www.bcdnetwork.com (September 16, 2009) by Mark Baker, Pres., IBA Consultants:
6. PMU is the acronym for Performance MockUp. Basically the distinction between “Visual” (VMU) and “Performance” models is that in a VMU is made just so the owner, contractor(s) and Design Team can visually inspect it to better judge how it will “look” in its final, erected form, whereas the PMU is made to be shipped to retained experts to “perform” a series of tests to see how the model reacts to the stresses and strains of later actual use. See generally Building Design & Construction (online magazine) at www.bcdnetwork.com
Metfab Metals has decades of experience producing all the various metal parts/assemblies needed for YOUR retro jobs that can serve to make them go smoothly from its earliest stages------------and end successfully!
Call us; you’ll soon see we produce.
Call me for ALL your METALS questions. If I can't answer it, I have all the needed "sources" to do so!
Jim Murray, C.O.O. 973-675-7676
[email protected]
October, 2016 Newsletter
Metfab Metals. LLC
Diversity----That Describes Our Product Line Too!
LET US BE PART OF YOUR DIVERSITY!!
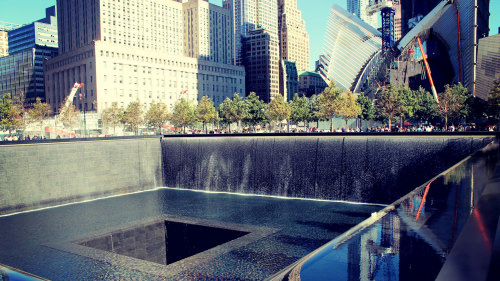
[Memorial Pool at the New World Trade Center, NYC, NY. We made the steel anchors within to hold this beautiful black granite.]
No metal fabricator has more expertise and more focused experience than Metfab Metals, LLC on a full spectrum of jobs. Good examples arise out the work we did at the restoration of Ground Zero after the 9/11 debacle. We not only built the VMU for WTC4, we built all the solid steel mullions for that 5-storey aerie or entrance podium. At the same time we were the fabricator that made the (now-concealed) anchors that secured the black granite slabs that form the basin of the Memorial Pools in the footprint of the original towers. [See picture above.] We are truly subscribers to DIVERSITY! In products, employment, jobs, projects, fellow citizens!
What is diversity?
Diversity is more than just integration. Diversity is a state of mind. Diversity is more than just enrollment percentages or a welcoming environment. Diversity exists when you go above and beyond being aware of differences or accepting differences to the point of actively including people who are different from you. Diversity is learning from our differences to make the whole community a better place. [Charis Redmond, Univ of Virginia, class of 2017, [http://www.law.virginia.edu/html/news/2016_spr/diversity.htm]. |
Ms. Redmond above was clearly talking about the scope of students and the effect of their diverse backgrounds on community life in Charlottesville. But, perhaps surprisingly, her words can apply otherwise, even to building great projects and their mundane constituent elements. Let me remind you of what talented, diverse architects are doing to otherwise very practical buildings based upon their own background.
By now, many of you have heard of the British architect, David Adjaye, AIA, who recently present to the world his masterpiece in Washington, DC: The National Museum of Adfrican American History & Culture. In itself, this is a metaphor or a testament to the concept of “diversity”. How? Just look at it.
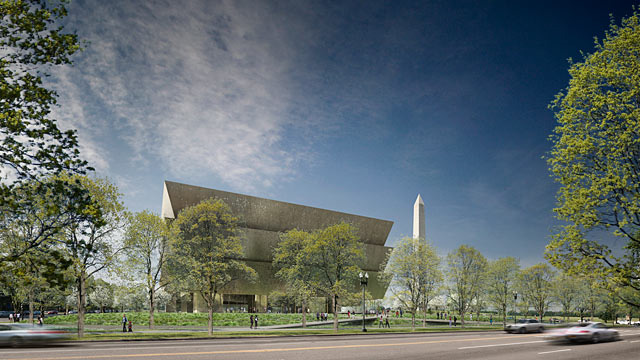
How is this inanimate building a true metaphor of diversity? Just look at the copper plaques that form the exterior of this new museum and trace the history of African Americans here in America (as these plaques hang affixed to the trusses & “bookshelves” we built right here at Metfab Metals, LLC). We were proud to be a part of this effort.
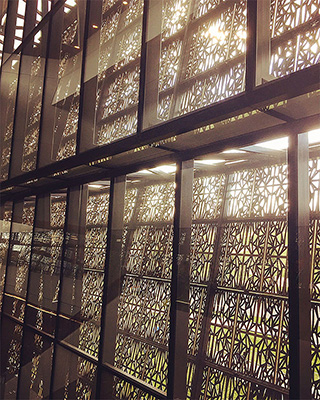
[The exterior of NMAAHC from the inside, showing trusses & “bookshelves” we built]
Look at our product line ---another example of diversity. “We make it all.” Once you do, send us an RFQ; you’ll be happy with what we can do for you---and do it fast, on time & on budget, per your specs.
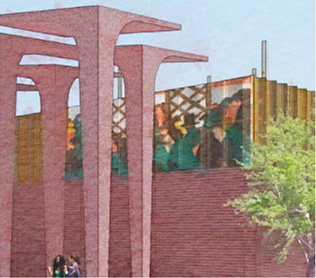
[David Adjaye's new conception for a power station right here in Newark, NJ---McCarter Sub-Station]
Just as Mr. Adjaye was so creative with the iconic, historic The National Museum of Adfrican American History & Culture in Washington, DC, he is bringing the same creativity & skills to this far more mundane power sub-station in the heart of residential Newark.
Metfab Metals has decades of experience producing all the various metal parts/assemblies needed for YOUR retro jobs that can serve to make them go smoothly from its earliest stages------------and end successfully!
Call us; you’ll soon see we produce.
Call me for ALL your METALS questions. If I can't answer it, I have all the needed "sources" to do so!
Jim Murray, C.O.O. 973-675-7676
[email protected]
September, 2016 Newsletter
Retro-Fit? Retro-Clad?----We Supply All the
Anchors & Misc Metals for These Jobs Too!
LET US MAKE THESE PARTS FOR YOU TOO
Many new projects are actually re-builds of sound older buildings that need to be brought up to current standards for one or more of myriad reasons. No metal fabricator has more expertise and more focused experience than Metfab Metals, LLC on such jobs. A good example is the full replacement of the exterior skin (or envelope) of the United Nations Building in NYC which we did a few years back.
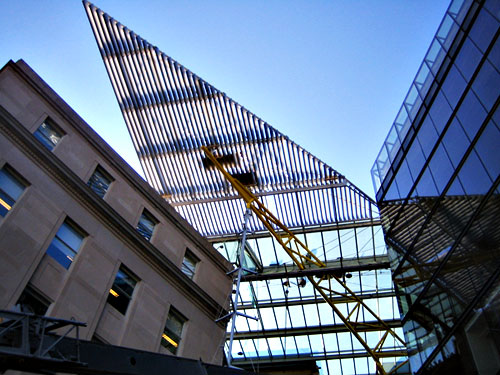
[“51 Louisiana”: Another Metfab Metals retro job ("roof ladder" covering) we did years ago in Washington, DC]
But what does this “retro-fit” actually mean? Well, a “retro-fit” or “retro-clad” job can take many forms, all defined by the specs issued for the project. Most simply, it can just mean furnishing new parts or equipment not available at the time of original construction. Or it can be a more full-blown tear-out where the building is stripped down to its super-structure and every system, covering, cladding and finish is replaced, often to adapt it to a new use or purpose. Regularly today, the purpose can be expressed in one word: GREEN, that is, the owners want to make the building far more energy efficient with power & maintenance savings offsetting much of the retro-fit costs. We are currently doing a major such job at Alexander Court in Virginia. This is a common project today, especially to gain better energy efficiency, gain more internal (expanded) space, adapt to a new use, re-purpose the entire building---and more. Such was the case recently with the century-old Tozzer Library at Harvard. Look what this archaic building turned into---and read the brief excerpt below as to such “building envelopes”.
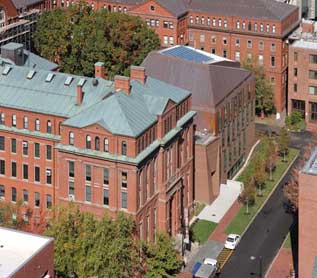 |
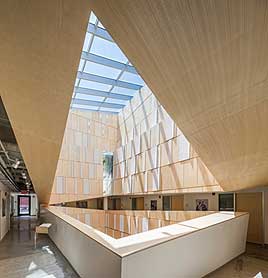 |
The importance of campus building envelopes is more than skin deep. That fact is becoming increasingly evident when it is time for repairs and renovations. Indeed, elements such as façades, windows, and roofs can importantly aid efforts to improve building performance.
Such efforts can be integrated. Upgrades to a building’s mechanical systems, for example, need to be accompanied by a close look at the building envelope because the latter can greatly impact the former. Craig Schwitter and Erik Verboon of Buro Happold, an engineering consulting firm, put it this way: “We are no longer in an age where we can pump energy into a building without the right envelope.” (1) |
As we here at Metfab Metals know our industry (& yours) and always focus on how we can better handle your job’s needs, this means we can---and do---supply ALL the metal products you need for such a ”retro” project. Currently, we are supplying various aspects of the fabricated metals for the Alexander Court re-styling of that preserved building in Alexandria, VA.
As this process of planning and spec’ing regularly starts BEFORE we are offered a PO for the final fabricated metal needed at the jobsite, (2) we ask our regular customers to involve us more in this planning stage. This is a NO-cost offer in which we take a look at what metals are needed and give the Owner & Design Team a chance to take advantage of our hands-on, current experience as to what works best in our aspect of the plans (yet to be finalized). Last month, here in this space, we talked about the value of VMU’s and PMU’s and how we offer that service. This is an item that can be considered a wise investment on many retro jobs. (3)
We often take an order for a VMU or PMU (4) at an early pre-construction stage so the design team can see exactly they want, perhaps see how it reacts to the elements and issue revised specs, drawings and PO’s along those adjusted lines. In our long experience, a VMU is an ultimately cost-effective way to qualitatively test whether your specs have a problem well-worth solving before committing to building out all the fabricated steel your design calls for, as well as ancillary parts such as glass, color, fillers, nuts & bolts and much more.
1. Building Design & Construction (online magazine) at www.bcdnetwork.com (September 16, 2009) by Mark Baker, Pres., IBA Consultants
2. Look again at how we have accommodated customers---and triggered cost-savings and error-avoidance with this modality.
3. PMU is the acronym for Performance MockUp. Basically the distinction between “Visual” and “Performance” models is that in the former it is made just so the owner, contractor(s) and Design Team can visually inspect it to better judge how it will “look” in its final, erected form, whereas the PMU is made to be shipped to retained experts to “perform” a series of tests to see how the model reacts to the stresses and strains of later actual use. See generally Building Design & Construction (online magazine) at www.bcdnetwork.com
4. College Planning & Management, Scott Berman, June 1, 2013.
Metfab Metals has decades of experience producing all the various metal parts/assemblies needed for YOUR retro jobs that can serve to make them go smoothly from its earliest stages------------and end successfully!
Call us; you’ll soon see we produce.
Call me for ALL your METALS questions. If I can't answer it, I have all the needed "sources" to do so!
Jim Murray, C.O.O. 973-675-7676
[email protected]
August, 2016 Newsletter
Metfab Metals. LLC
VMU’s
----“Visual Mock-Ups”--- All Kinds
LET US MAKE YOUR PRE-CONSTRUCTION MODELS TOO,
AS WE HAVE DONE FOR SO MANY
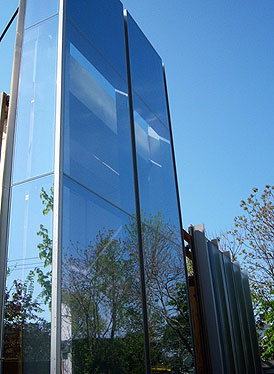
[ VMU we made for WTC4 during the rebuilding of Ground Zero after 9/11]
When your project specs a VMU, even with specialty AESS (1) FRAMES, no one has more expertise and longer experience than Metfab Metals, LLC. Few can give you the option of erecting it at their yards, “dry-fitting” for pre-welding inspections (see illustration below), delivering in modular parts or welded/assembled/finished to your jobsite or delivering it to your designee to be tested as a “PMU” (see footnote #4 below).
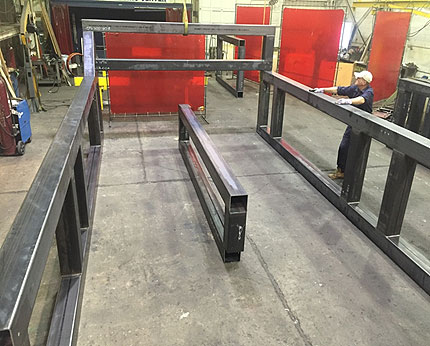 |
VMU being "dry-fitted" here for the "BORO” development in Virginia. This way, we know the modular parts shown will fit perfectly when they arrive at the jobsite for assembly & welding there, just as ordered. Just shipped in August, 2016.[These elements can also be finished to AESS (2) standards, a process we have have worked with now for 30+ years.] |
But how does this fit with your job needs? As we here at Metfab Metals know our industry (& yours) and always focus on how we can better handle your job’s needs, this means we can---and do---supply ALL the metal products you need. And this regularly starts BEFORE we get a PO for the final fabricated metal needed at the jobsite. (3)
"For those not familiar with curtain wall mockup testing, it involves constructing a full-scale, representative section of a curtain wall system and subjecting it to a battery of tests prior to full-scale production of the curtain wall components. It is important to perform the mockup testing well in advance of fabrication, assembly, and installation so that any design changes can be incorporated into the production of panels.
Typically, the test specimen is selected by the curtain wall consultant or architect to ensure it incorporates all critical components of the curtain wall, including stack joints, inside and outside corners, operable vents, maximum glass sizes, and mullion spans. The consultant or architect will also develop a test procedure, which almost always includes air infiltration testing, water penetration resistance testing (using both static and dynamic pressures), and structural load testing.” [Building Design & Construction (online magazine) at www.bcdnetwork.com (September 16, 2009)] |
We often take an order for a VMU or PMU (4) at an early pre-construction stage so the design team can see exactly they want, perhaps see how it reacts to the elements and issue revised specs, drawings and PO’s along those adjusted lines. In our long experience, a VMU is an ultimately cost-effective way to qualitatively test whether your specs have a problem well-worth solving before committing to building out all the fabricated steel your design calls for, as well as ancillary parts such as glass, color, fillers, nuts & bolts and much more.
Metfab Metals has decades of experience making these Mock-Ups and making YOUR jobs go smoothly from its earliest stages------------and end successfully! Call us; you’ll soon see we produce.
1. PMU is the acronym for
Performance
Mock
Up. Basically the distinction between “Visual” and “Performance” models is that in the former it is made just so the owner, contractor(s) and Design Team can visually inspect it to better judge how it will “look” in its final, erected form, whereas the
PMU is made to be shipped to retained experts to “perform” a series of tests to see how the model reacts to the stresses and strains of later actual use. See generally
Building Design & Construction (online magazine) at www.bcdnetwork.com
2. Building Design & Construction (online magazine) at
www.bcdnetwork.com (September 16, 2009) by Mark Baker, Pres.,
IBA Consultants:
3. See also: CISC Guide for Specifying Architecturally Exposed Structural Steel. Canadian Institute of Steel Construction, 2012, 2nd Edition, Page 7, primarily authored by Terri Meyer Boake, , B.E.S., B. Arch., M. Arch., LEED AP. We are grateful to her and this resource for all its very useful insights and clarity. This is a useful tool in both explaining this art, as well as drawing accurate specifications.
4.AESS is Architecturally Exposed Structural Steel, and is finely-finished steel members (prepped, welded, filled, blasted, polished, and/or uniquely painted/finished) to be permanently open to the view and touch by all after the job is done.
Call me for ALL your METALS questions. If I can't answer it, I have all the needed "sources" to do so!
Jim Murray, C.O.O. 973-675-7676
[email protected]
July, 2016 Newsletter
“SAMPLES”
Another Metfab Metals
Idea
to Better Guarantee Accuracy
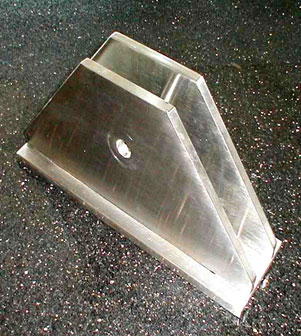 |
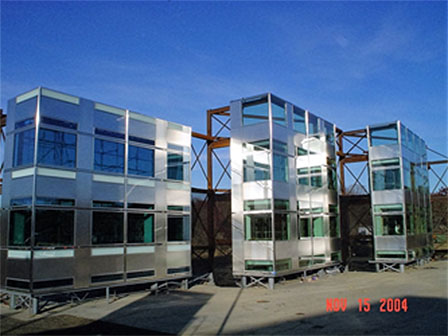 |
In recent years, in our monthly Newsletters, as well as on our website,we’ve told you about our wide range of our capacities. We make all the standard steel parts & assemblies, can handle and deliver AESS (1), fabricate Major Mullions, finish all products exactly as you spec them, and make any other steel specialty products that your job specs call for. Following up on what we said about our capacities to produce AESS, (2) we’d now like to tell you a little about something we do, often totally at our own expense but always to accommodate our customers’ real needs. We make samples, yes SAMPLES!
This may be especially critical for you, due to the uniqueness or demanding narrow tolerance of your job’s design.
What do we mean by this? Let me illustrate: recently a customer ordered close to a thousand custom anchors. These were not large anchors, but they were very specific in their custom design. Jim looked at the drawing and just sensed that it was somehow “wrong”! But we had both a P.O. and an approved drawing (with a specified finish also). We had some lead time so we could have made these at a more leisurely pace, packed them, shipped them and billed them. That would have been 100% appropriate compliance with “what the customer ordered”. But experience told Jim something was “off” about the drawing and further told him how to address this concern in the best way for all involved.
What was this chosen remedy? Simple: make a sample!
So the shop ginned up a fully drawing-compliant anchor; Jim Fed-Ex’d this free sample overnight to the customer and got a call before noon the next day. “Don’t make any more of these yet. They’re backwards.” The drawing had somehow been made in a mirror-image of what was needed! The P.O.-compliant sample had all the holes, bends and fittings basically 180 degrees removed from where they had to be in order to “fit”. Had we made the whole order, the customer would have had ONE THOUSAND (1000) useless anchors instead of ONE! So we got a corrected drawing and timely made the RIGHT anchor. Result: we wound up with a happy customer instead of a frustrated one. And our happy customer wound up with a timely delivery of perfectly-useful anchors that made his job go smoothly (at least in this regard)!
[A similar situation arises in many larger projects, where the specs themselves stipulate a far larger “sample” as they require from us a VMU (Visual Mock-Up) (3), largely so that the owner, architect, design team and others can SEE a full section of the building, as it will actually appear later, with all our finished specialty products (fully-assembled & erected), with glass and variant finishes down to the fine details.] In effect, this is just a large-scale SAMPLE.
We here at Metfab Metals don’t produce samples for every order; it’s often not cost-efficient for us or the customer; NO fabricator does otherwise! But, in the appropriate situation, we can give you a real-time look at how your unique item or fabrication will appear in finished condition, especially where you need many of one unique type that, in total, are fairly expensive.
This may actually be a cost-effective solution when the part, assembly or even an entire building section (e.g., VMU) is innovative to such a degree that the Design Team wants “hands-on” contact with what has been drawn to better judge if this aspect of the design is truly best, has the esthetic appearance sought-----or even just all “works” together. A working “sample” (large or small) can end your concern about this aspect of the overall job and result in these specialty parts later arriving at your jobsite in installation condition, as hoped/designed.
Metfab Metals has decades of experience solving problems before site-delivery. Our many regular customers know our capacities go beyond rote fabrication, handling and delivery. For many owners, only the end-product is of enduring concern. Needless to say, we realize this and have refined our in-house and outsourced skills to be able to deliver any sample or “appearance” you want or your architect draws. No other fabricator can better deliver the broad array of these true “fits” in easy installation condition, day in, day out.
*************************************************************************************
Watch for future updates in our Newsletters and emails.
*************************************************************************************
We always offer to work with our customers from the job concept stage to anticipate issues before fabrication, to suggest better ways to order, extrude, cut, drill, paint, finish, even stage and deliver and always to save time and money.
1. AESS, or Architecturally Exposed Structural Steel, is what we have now literature as finely repeated many (to some of you regular readers TOO MANY) times in our -finished steel members (prepped, welded, filled, blasted, polished, and/or uniquely painted/finished) to be permanently open to the view and touch of all after the job is done. AESS work is never covered by sheetrock or otherwise hidden from public view.
3. “VMU” stands for Visual Mock-Up. We have made many of these pre-construction (smaller-scale often) models of building segments so that the design team, owner, GC and others can see first-hand what the erected product will look like, even varying finishes, caulking, fenestration, and the like on such a model so all can better judge what the presented alternatives best suggest. Often we erect these VMU’s right here in our yard as a service to our customers. Or we can make a “portable” VMU so that it can be viewed at the building’s site itself.
Call me for ALL your METALS questions. If I can't answer it, I have all the needed "sources" to do so!
Jim Murray, C.O.O. 973-675-7676
[email protected]
June, 2016 Newsletter
Specialists in Podium Steel & Major Mullions
ONLY FABRICATORS WITH THE BACKGROUND, DECADES OF
EXPERIENCE AND PAST SUCCESSES ARE EVEN ASKED TO MAKE THESE
HUGE MULLIONS! FABRICATORS LIKE Metfab Metals, LLC.
LET US TAKE CHARGE OF YOUR PROJECT’S OWN DESTINY FROM THIS EARLY STAGE!!!
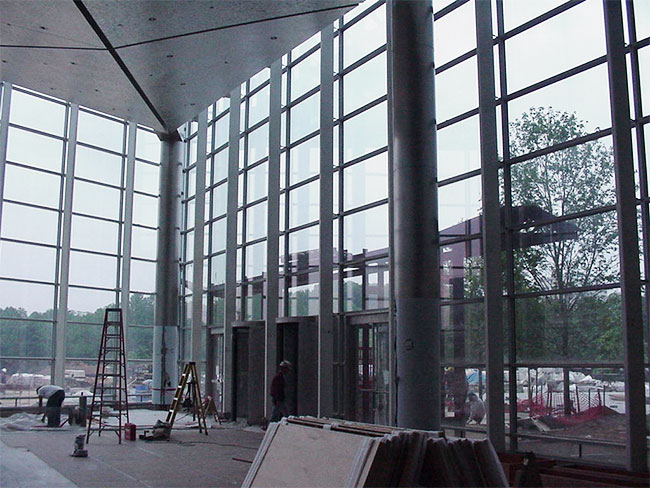
[The PRODUCTION TEAM we have assembled in the last 30 years has worked diligently on all types & variations of PODIUM STEEL/MULLIONS for you, in varying degrees and proportions, as the individual job needs dictated. We have all been doing this work now for over THREE DECADES.
When it comes to PODIUM STEEL, even with specialty EXTERIOR FRAMES and related parts, no one has more expertise and longer experience than Metfab Metals, LLC.
Most of these elements are finished to AESS standards, a process we have have worked with now for 30+ years.
AESS; Shop Assembly of your Parts;Mullions of all Dimensions; Embeds; Specialty Packaging; Timed/Staged Deliveries (by floor or elevation, as you direct)!
Here’s the way we here at Metfab Metals, LLC often offer these (and many others):
|
- Major Mullions;
- All sizes: 6” thick to 60’ long;
- SOLID Steel Mullions;
- ALL five (5) AESS categories (or special order);
- Machined & Completely Finished; Ready for curtainwall attachment;
- High Performance Paint or custom finished, as spec’d;
- Packaging (specialty by floor/elevation);
- Timed/Spaced Deliveries;
- All the above logically saves YOU costs--$$$--with no onsite assembly & full QC of assembly here BEFORE shipment/packing.
|
These are the nine (9)essential steps—the "Metfab Metals Podium/Mullion Process”, if you will —presenting what you need for your job specs/site needs/contract compliance. [Look at the attached Gallery of Pictures for real-time illustrations.]
But what does this all mean to you, our customers, here at Metfab Metals? It means we know our industry and always focus and learn so that we better handle our common marketplace and the metal products you need. We do this so that we can fulfill all your metals needs.We daily implement/use better methods, better processes, better subcontractors, better technology, and better records of how we did it all.
Metfab Metals has decades of experience making these products and making YOUR jobs go smoothly and end successfully! Call us; you’ll soon see what we have written here is what happens there.
Call me for ALL your METALS questions. If I can't answer it, I have all the needed "sources" to do so!
Jim Murray, C.O.O. 973-675-7676
[email protected]
May, 2016 Newsletter
COOPERATION----THE standard at Metfab Metals
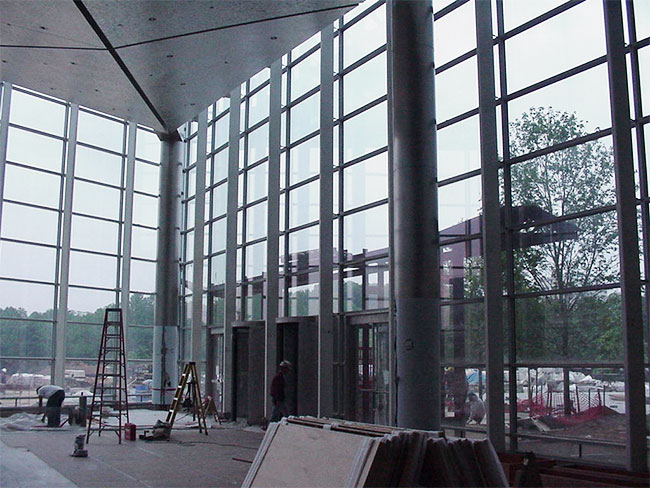
[One of our jobs, as we worked closely to supply the fabricated steel exactly as spec’d.]
Computers have been called our “New Kind of Co-Worker”; more correctly, it’s their programs that assist us so much, maybe especially in this industry. In metal fabrication, this may also be even truer of our shop functions than our office functions.
How so? You ask! Just think of how much precision a computer-driven plasma cutter adds---and how much time its saves. That means better compliance with job specs, a consequently smoother installation process and, ultimately, cost savings on the job. And the plasma cutter is not the only industry process running better because of what computers can do so easily.
A few years back I read an electronic article from WPL on “Shop Drawings”. [I believe it was in one of their ads in 2014.] It said:
“Design professionals are generally responsible for plans and specifications, while contractors are responsible for the means and methods they employ to construct a project. Construction details are often produced by contractors and their subcontractors, however, and reviewed by the design professional before being utilized. In this manner, constructors and subcontractors may venture into the design process and subject themselves to its attendant risks and liabilities. The production and use of these “shop drawings” involves a carefully orchestrated flow of papers, and attention to each party’s proper role is important for minimizing risk.” |
Guess who the un-mentioned “New Kind of Co-Worker” who is not identified there but clearly must be inferred in that article? Yup, our ubiquitous computer programs, especially those with CAD capabilities.
Reading all of this together leads to yet another conclusion we are all wise to understand from the getgo in a large project ---- Cooperation is the sine qua non or indispensable essential for success in building. Without such cooperation (read: job transparency), problems will arise and likely fast multiply.
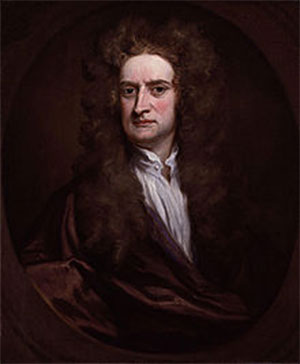
[This is not our founder but rather a much older fellow, as we will explain below.]
[Metfab Metals has been around a long time, but not THAT long!]
Most of you may recognize at least the name of Sir Isaac Newton, the 17th-century English math genius (pictured above) who developed the original statements of the Law of Gravity and the Laws of Motion, transformed the science of optics and literally created Infinitesimal Calculus. But it was his basic insistence on order and clarity in all science, as he opposed explaining “WHY” things do what they do, that is perhaps his most lasting legacy. What he simply wanted to show was HOW things worked.
Why do we here at Metfab Metals quote all this to you? The reason is simple: we too like “order and clarity” in what our customers need and we always insist upon knowing HOW we are to produce it for you. So a seldom-recited quote from Newton makes a good point for us now, even after three (3) centuries!
“Tact is the knack of making a point without making an enemy.”
So we too want to make a point to you---tactfully! Newton insisted that truth is more readily found in simplicity, and not in the multiplicity and confusion of things. This led to his monumental successes; but it can lead to our success together too. The key is COOPERATION! We simply want you to get us involved early in the aspects of your jobs where we have the expertise.
And don’t forget our unique offer:
We always offer to consult—for free--with our customers from the project concept stage to anticipate issues before fabrication, to suggest better ways to order, extrude, cut, drill, paint, finish, even stage and deliver and always to save time and money.
Call me.
Jim Murray, C.O.O. 973-675-7676
[email protected]
April, 2016 Newsletter
Metfab Metals. LLC
Accuracy in Drawings & Specs — Truly A
Cost -
Savings Step!
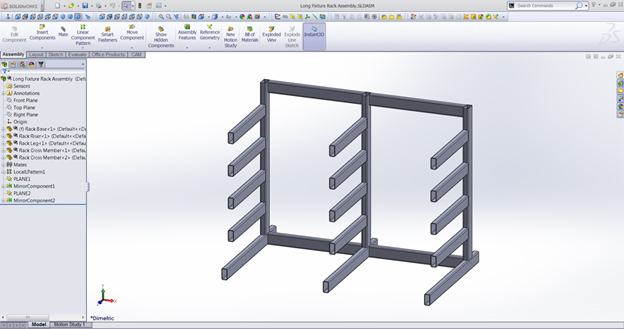
[SolidWorks---we can produce in-house 3-D fab drawings like this from
ACCURATE specs or models electronically sent to us!].
In recent years, we have almost preached here the cost savings of accurate “Plans & Specs”, more specifically how these can enable us to make better “fab” drawings to produce mullions, anchors, parts & assemblies that will “fit” precisely when they get to your jobsite. Now THAT leads to palpable cost-savings for you, us and the Owner, leading in turn to universal job cost savings and better customer relations!
Now, we see that Modern Steel Construction dedicated two full articles in one edition to this general topic. 1.
A brief excerpt tells us a lot:
[As to “a good design drawing”…… “most people ….refer to …..”theCode of Standard Practice” which states:
“The contract documents provide complete structural steel design plans clearly showing the work to be performed and giving the size, section, material grade, and the location of all members, floor levels, column centers and offsets, camber of members, with sufficient dimensions to convey accurately the quantity and nature of the structural steel to be furnished. …….[C]ritical requirements affecting the integrity of the structure necessary to protect the owner’s interest must be covered in the contract documents.” 2. |
Due to almost-amazing capabilities of programs like SolidWorks and Autodesk’s Inventor (among others), we can now electronically (& instantaneously) accept incomplete drawings, if accompanied by detailed specs and a 3-D model. Take-offs from these, we can now do in-house. Call us; we can explain more. You can appreciate that this can substantially increase the pace of a job----or make up for time lost at earlier stages due to unanticipated, extended contracting, bidding, quoting or whatever.
Later in the same magazine there are listed 10 “tips” as to what good contract documents should include to accurately spec the sub-contractor’s work and fulfill the owner’s expectations.3.
We routinely generate 3-D drawings for our shop staff to view as they make the specified parts. That this fulfills the old idea that “a picture is worth a thousand words” is evident everyday here at Metfab Metals.
3-D computerization has transformed the exchange of information in our industry. Now we should all implement the daily use of this capacity as its serves all our interests, and ultimately saves time, eliminates errors, avoids producing non-compliant parts---and saves wasting costs needlessly. The Modern Steel Construction articles conclude with this spot-on observation:
“……The key is developing your system to have your pricing to be competitive yet not sacrifice quality and still get the job done in the time frame that is wanted…….” 4.
This admonition is particularly applicable when specifying AESS parts & components:
[AESS is Architecturally Exposed Structural Steel, and is finely-finished steel members (prepped, welded, filled, blasted, polished, and/or uniquely painted/finished) to be permanently open to the view and touch by all after the job is done. ] 5.
The design, detailing and finish requirements of AESS will typically exceed that of standard structural steel normally concealed by other finishes. 6.
All of us in the construction industry are well-advised to understand this concept better as there are “categories” of this finish which greatly vary the work required----and therefore the cost.
|
But what does this all mean to you, our customers, here at Metfab Metals? It means we know our industry and always adjust and learn so that we better handle our common marketplace and the metal products you need. We do this so that we can fulfill all your metals needs.We daily implement/use better methods, better processes, better subcontractors, better technology, and better records of how we did it all.
Metfab Metals has decades of experience making these products and making YOUR jobs go smoothly and end successfully! Call us; you’ll soon see what we have written here is what happens there.
Call me for ALL your METALS questions. If I can't answer it, I have all the needed "sources" to do so!
Jim Murray, C.O.O. 973-675-7676
[email protected]
1. Modern Steel Construction (magazine), February, 2015, pgs 17-27; 50-51 published by AISC, One East Wacker drive, Chicago, IL 60601
2. See footnote #1 at p. 50.
3. Again---- footnote #1 at p. 50.
4. Again---- footnote #1 at p. 51.
5. An even more precise definition is:
Architecturally Exposed Structural Steel (AESS) is steel that is designed for structural sufficiency to meet the primary needs of the building, canopies or ancillary structures, while at the same time remaining exposed to view. It is therefore a significant part of the architectural language of the building.
6. CISC Guide for Specifying Architecturally Exposed Structural Steel. Canadian Institute of Steel Construction, 2012, 2nd Edition, Page 7, primarily authored by Terri Meyer Boake, B.E.S., B. Arch., M. Arch., LEED AP. We are grateful to her and this resource for all its very useful insights and clarity. This is a useful tool in both explaining this art, as well as drawing accurate specifications.
March, 2016 Newsletter
AESS UPDATED
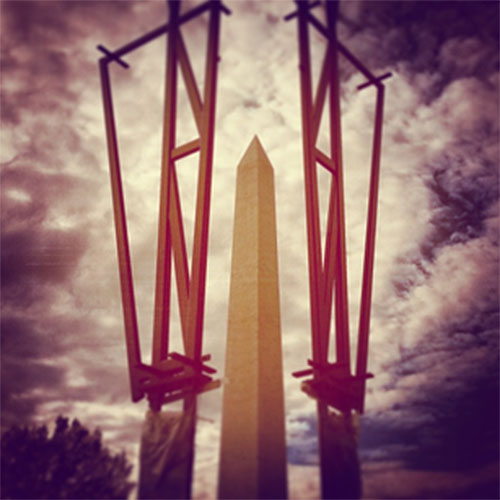
[NMAAHC---as under construction—now due to open in September, 2016]. |
Last March, we announced in this space our final deliveries for the external frames at the Washington, DC National Museum of African American History & Culture (“NMAAHC”) with the above candid shot, an actual view of one of the final days of erection. That was a huge landmark in AESS for us.
As we have reported in this space many times before, we have been fulfilling AESS orders for customers for over 20 years. Our first MAJOR job we fulfilled was at BWI Airport (Thurgood Marshall BWI Airport) just outside Baltimore, MD. We made all the elements for the ceiling web of inter-connecting sky-frames that still gleam over 20 years later now. Take a look the next time you are passing through. Till then look at their picture below.
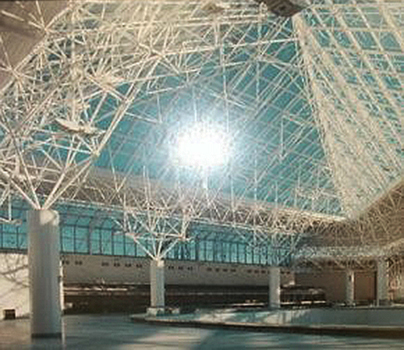
[Thurgood Marshall BWI Airport--our AESS
fabrications erected in mid-1990’s]
A brief excerpt as to our current 2016 state-of-the-art level of AESS skills well illustrates what information we can now put at your finger tips:
AESS is Architecturally Exposed Structural Steel, and is finely-finished steel members (prepped, welded, filled, blasted, polished, and/or uniquely painted/finished) to be permanently open to the view and touch by all after the job is done.
An even more precise definition is:
Architecturally Exposed Structural Steel (AESS) is steel that is designed for structural sufficiency to meet the primary needs of the building, canopies or ancillary structures, while at the same time remaining exposed to view. It is therefore a significant part of the architectural language of the building. The design, detailing and finish requirements of AESS will typically exceed that of standard structural steel normally concealed by other finishes. 1.
All of us in the construction industry are well-advised to understand this concept better as there are “categories” of this finish which greatly vary the work required----and therefore the cost.
This Guide (see footnote #1 below) was developed to facilitate better communication among architects, engineers and fabricators. It was felt that visual references would help all parties understand the intent of the new AESS documents as applied to the design of structures. 2.
AESS work is never covered by sheetrock or otherwise hidden from public view. During construction, or even after the structure is complete, at any floor level or at ground level, one can walk up to this steel member, examine it, touch it, see all its perfection or imperfections [as either can be specified per one of the five (5) categories (grades) of AESS commonly available, and detailed in the manual referenced in footnote #1. |
At Metfab Metals, we have found that looking back provides a good way to measure whether---and how much---progress we have made toward 100% customer satisfaction. Looking again through our website and all our archived Newsletters has made us realize how much better we can tell you all that is available from us and how.
But what does this all mean to you, our customers, here at Metfab Metals? It means we know our industry and always adjust and learn so that we better handle our common marketplace and the metal products you need. We daily implement better methods, better processes, better subcontractors, better technology, and better records of how we did it all.
Metfab Metals has decades of experience making these parts and making YOUR jobs go smoothly and end successfully! Call us; you’ll soon see what we have written here is what happens there.
Call me for ALL your METALS questions. If I can't answer it, I have all the needed "sources" to do so!
Jim Murray, C.O.O. 973-675-7676
[email protected]
1. CISC Guide for Specifying Architecturally Exposed Structural Steel. Canadian Institute of Steel Construction, 2012, 2nd Edition, Page 7, primarily authored by Terri Meyer Boake, , B.E.S., B. Arch., M. Arch., LEED AP. We are grateful to her and this resource for all its very useful insights and clarity. This is a useful tool in both explaining this art, as well as drawing accurate specifications.
2. Ibid. at page 7 also.
February, 2016 Newsletter
Always Your “AESS Preferred Vendor”
With Efficiency Comes Capacity
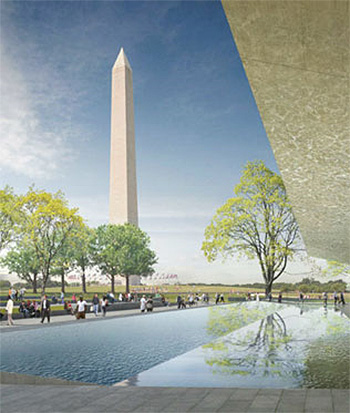 |
This project in which we worked so closely with our customers, Enclos Corp. & Northstar Contracting, has now won numerous aesthetic awards, many related to the steel we supplied, with marvelous finishes.
These were awarded by the Washington Building Congress as below:
- Exterior Glass (Enclos);
- Specialty Painting (Northstar);
- Ornamental Metal (Northstar);
- Structural Steel Framing (Enclos).
We congratulate our customers and add that we are happy to have provided some of the services that underpin these recognized accomplishments. |
Figure 1 This illustrates how closely this new icon
is to a very recognizable icon. |
At the end of 2015, we told you in this space of the UAV’s or construction “drones” that are fast becoming commonplace at construction sites world-wide. Below we want to tell you what is about to become an icon in Modern America, now in the final phases of pre-opening outfitting.
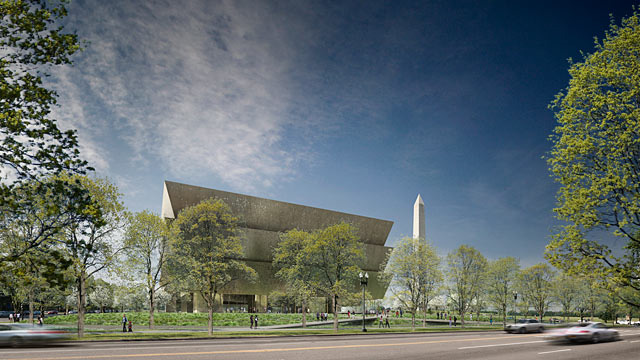
From our vantage point, as the supplier of some of the critical steel building elements---and finishes---pictured above, we view these awards as a proverbial “pat on the back” for our work. As with all such huge and public projects, there were the “speed bumps” with original plan development, spec adjustments after contracting and problems beyond our agreed scope which we worked out without delivery delay. We offered even execution solutions in incremental steps to make the project go forward----and on schedule.
As we like to say, we here at Metfab Metals always look to our customers to integrate us into their processes, even at the design & planning stages, to save time and avoid delays.
Now Enclos and our other customer here (Northstar, Cleveland, OH) are worthy recipients of these awards, and deservedly so. We are just happy that we worked so closely with them to supply the AESS steel in pristine condition, ready to install, so that they could become candidates for these recognitions by their industry peers.
What do we draw from this? Simply----while Metfab Metals does not install at the jobsite, we always work, side by side, with our customers to make their work on-site easier, better and in full conformance with the plans & specs. . We already have in place all the technology---and informed staff---to make this all smooth and workable from the getgo.
Call us; you’ll soon see what we have written here is what we really can do for you.
Note to our readers: Watch for future updates. [If we don’t have your company’s current list of project managers, as well as others, send it to us.] We can’t send you these informative posts, if we don’t have ALL your contact information---and that of ALL your project managers.
Call me for ALL your METALS questions. If I can't answer it, I have all the needed "sources" to do so!
Jim Murray, C.O.O. 973-675-7676
[email protected]
We always offer to work with our customers from the job concept stage to anticipate issues before fabrication, to suggest better ways to order, extrude, cut, drill, paint, finish, even stage and deliver and always to save time and money. |
January, 2016 Newsletter
HAPPY NEW YEAR & SUPER SUCCESS IN 2016
METFAB METALS' SUPER-SUCCESS IN 2016? MORE
NEW TERRIFIC CUSTOMERS LIKE YOU
This is the time of year when many of us make resolutions to do better things in the New Year! Many of those “commitments” are soon put aside---especially if they involve weight loss and/or healthy eating. Our company resolution will NOT be put aside. Not just one of us here is committed to it: WE ALL ARE!
So what is this firm resolve of ours? Simply to do MORE!
What is our idea of “more”?
More sales; more great projects; more good work for you, our customers (whether you have been a customer for decades---as many are—or you are just trying our announced skills, proclaimed expertise, even new ideas!
Let me give you a brief “window” into Metfab Metals’ capacities, 2015 advances and the actual systems we use daily to timely and accurately deliver even on the most detailed and spec-demanding projects-----on your jobs, large and small alike!
In past Newsletters (even before 2015----all archived on our under-reconstruction website at www.metfabmetals.com) we have stressed some truly unique AESS (1) jobs we have done. But we do the mundane, every-day metal fabrication too—and are happy to get your orders for this work.
Over the years we have talked briefly (or not so briefly at times!) in these media about our capacities, advances and systems in place (or planned) to deliver whatever you need in metals fabrication!These past few years Metfab Metals was challenged by the newest Smithsonian museum (NMAAHC) (2), where we met really challenging logistical, engineering and even documentation specs required to successfully complete this signature project. (3) Metfab Metals has been making small and large AESS parts for more than two (2) decades now, but this growing art form has now expanded into ever more uses and applications. NMAAHC might best be described as the “highest and best” use of this art-----as it runs throughout the entire structure, even outside forming the superstructure of the façade on all four (4) sides. It is indeed steel made to look like extruded plastic, molded to a purpose plastic could never fulfill. These facades are now there for you to see, live or via its website! www.nmaahac.org.
In the building business, how you see thingstruly depends upon the equipment you have with which to “see” them. Just think about how Excel, CAD and 3-D drawings let you “see” things you might have had trouble even conceptualizing just 10-20 years ago! We are daily using our proliferating office---and shop--- technology to meet the rigorous demands of both production and documentation for this NMAAHC project. We didn’t fail, nor will our technology ever be found wanting. We had literally prepared for this job for over twenty years. In these years we have made whatever the customer’s metal fabrication plans required: AESS to Major Mullions to huge stone anchors, trusses and many other specialty metals products. (4) The knowledge and skills we acquired over the years now make us fully equipped and able to meet any fabrication, spec or transparency need your job stipulates.
So what does this mean to you for 2016, as our customers here at Metfab Metals? Well, it means we have adjusted, learned and understood our marketplace, our industry and----most of all---you, our customers. So much so that we can fulfill all your fabricated metals needs---simultaneously meeting any special conditions of your project such as documentation, certifications (5), packing, timing, delivery and so much more.
What we also have right now is the added capacity and staff to handle even more for you. Let me tell you how: we have a new huge production shop, new equipment and even new experienced staff----all to make better parts, better buildings and better records of how we did it all (y’know: the oft-dreaded spec of “transparency”).
In this way, Metfab Metals has shown throughout 2015---and even before, and will show for you in 2016, that we are “team players” who want to be part of your regular building team, even the design team, of YOUR jobs so that together we can anticipate for you potential production snafu’s as well as erection issues so we can smoothly deliver precision products to become integral parts of truly memorable and lasting buildings------and do it all timely, with a minimal—or none at all--- change orders.
Metfab Metals has decades of experience making custom metal parts and making YOUR jobs go smoothly and end successfully! Call us; you’ll soon see what we have written here is what happens there.
UPDATE:
Hudson Yards, NYC, NY ----- We have been working here throughout 2015.This formerly-vacant several square blocks of in-city railroad storage, up on the West Side of Manhattan has required both the sophisticated and the mundane; everything from common anchors to classic AESS solid steel mullions, very similar to the same huge pristine mullions we delivered to WTC4 last year.
We always offer to work with our customers from the job concept stage to anticipate issues before fabrication, to suggest better ways to order, extrude, cut, drill, paint, finish, even stage and deliver and always to save time and money. |
Call me for ALL your METALS questions. If I can't answer it, I have all the needed "sources" to do so!
Jim Murray, C.O.O. 973-675-7676
[email protected]
1. AESS, or Architecturally Exposed Structural Steel, is what we have now defined many (to some of you regular readers TOO MANY) times as finely -finished steel members (prepped, welded, filled, blasted, polished, and/or uniquely painted/finished) to be permanently open to the view and touch of all after the job is done. AESS work is never covered by sheetrock or otherwise hidden from public view.
2. This is our daily shorthand for the rising National Museum of African American History & Culture which now occupies the last lot on the mall facing the Washington Monument. See www.nmaahc.org for a really impressive video and overview of this truly 21st century edifice!
3. We joked (only half-kiddingly) that, at the end of this job, the weight of the paper we have generated would exceed the steel we delivered----even though the actual fact is that the total steel will exceed TWO (2) MILLION pounds!
5. Metfab Metals is an SBE, SAM-certified, AWS-certified and regularly works in tandem with a WBE to meet any specification or set-aside your particular job has! We are also a member of GANA and AISC. We are prepared to meet your project’s most stringent spec.